For any company operating in the pharmaceutical sector and involved in manufacturing and/ or importing human and veterinary medicines, the Good Manufacturing Practice (GMP) is the closest thing to a holy book in the industry. It ensures that products are consistently produced and controlled according to quality standards, minimizing the risks involved in any pharmaceutical production. As such, it is essential for any company in the sector to adhere to GMP guidelines to guarantee the safety, efficacy, and quality of their products. The European Union GMP guidelines refer several times to a term which at first may seem confusing to someone not familiar with the terminology specific to the pharmaceutical industry – a quality agreement. What is hiding behind such an enigmatic TQA name? – a tool proven to be a valuable instrument while dealing with any GMP-related operations.
In today’s blog article, we will discuss the topic of quality contracts in the pharmaceutical industry. You’ll learn why such agreements are crucial to ensuring the safety and effectiveness of medicines. We will also look at the important aspects of such contracts and what benefits they can bring to pharmaceutical companies. Are you curious? I invite you to read!
What is a quality agreement?
A Quality Agreement, or in other words, a technical agreement, or technical quality agreement (TQA), has been defined by the US Food and Drug Administration (FDA) as a “comprehensive written agreement between parties involved in the contract manufacturing of drugs that defines and establishes each party’s manufacturing activities in terms of how each will comply with cGMP”[1]. A quality agreement identifies all relevant quality aspects and defines the roles and responsibilities of interested parties. As a general rule, a quality agreement should be placed between the entities involved in the outsourcing of even the tiniest bit of the medicinal products’ manufacturing process. Such entities are usually either contract givers (commissioning a service, product, project or study) or contract acceptors (agreeing to provide a service, product, project or study according to the contract givers’ specified requirements). Therefore, the quality agreements with the API Suppliers, Excipients Suppliers, Raw Material Suppliers, Packaging Material Suppliers, Contract Manufactures for Pharmaceuticals, Contract Laboratories, Distributors, Transportation Providers, Warehouses or IT Suppliers have to be concluded in accordance with Good Manufacturing Practices. Nevertheless, the need for conclusion of the quality agreement must be evaluated as part of the supplier qualification process.
The quality agreements should be written in a manner ensuring full transparency – each role and responsibility, including communication processes and timelines should be fully clear and understood by each party – the contract giver and the acceptor. The value of a common understanding in the field of quality cannot be overemphasized, as it is crucial to protecting patients’ health. In order to fully conform to the current GMP (cGMP), there is no room for ambiguity – according to the EU GMP guidelines, the contract should describe clearly who undertakes each step of the outsourced activity[2].
What falls within the scope of a quality agreement?
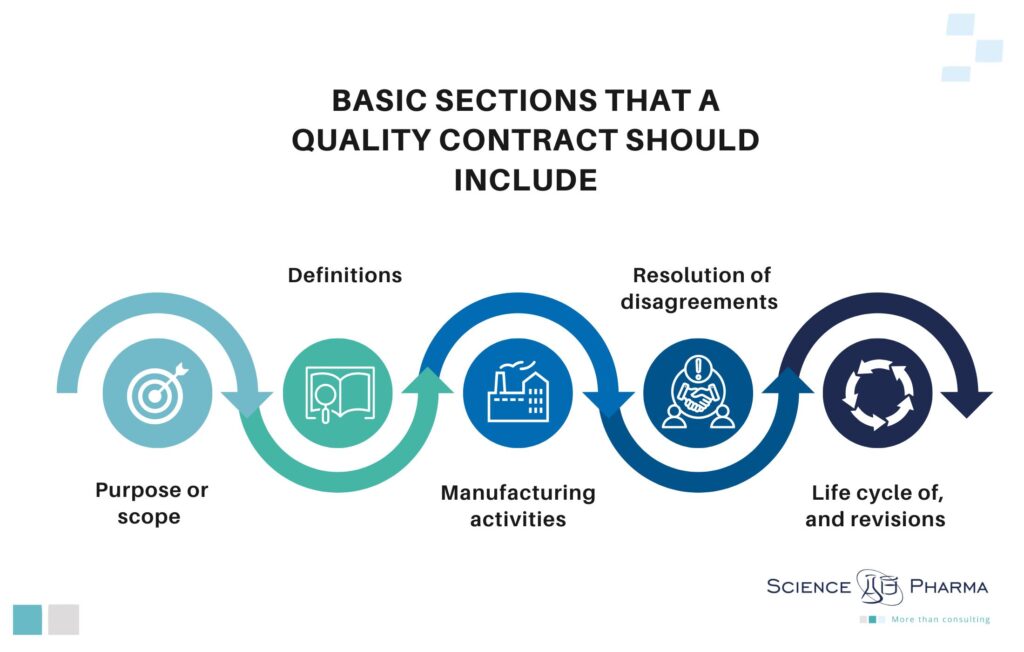
The purpose of a quality agreement is to explicitly assign specific GMP activities to particular parties thereto. In terms of the legal construction of the contract, according to the FDA’s recommendations[3], a quality agreement should include at least the following sections:
- purpose or scope – to precisely cover the extent of the services to be provided;
- definitions – to make sure that the parties are aligned on the exact meaning of terms in the agreement;
- manufacturing activities – to document activities associated with manufacturing processes;
- resolution of disagreements – to explain how the parties will resolve disagreements about, for instance, product quality issues;
- life cycle of, and revisions to, the quality agreement.
Taking into account the substantive content of the quality agreement, the quality agreement should define the system and processes by which manufacturers and suppliers of material/services manage the quality aspects of drug manufacturing and controls. Even though each contract has to be adjusted individually, the quality aspects, which should be considered during the determination of cooperation are as follows:
- International laws, rules and regulations,
- Licenses, certifications, requirements regarding standards and regulations,
- Quality assurance and control responsibilities,
- List and definitions of the contract material/product/services with reference to specifications, requirements,
- Change control process including approval process by contract giver,
- Management process of deviations, investigations, CAPAs, and OOS results,
- Test results, including approval requirements,
- Complaint handling procedures and demand CAPAs for issues,
- Contract giver right to conduct audits and demand CAPAs for issues,
- Audit access for notified bodies and contract givers,
- Information flow requirements,
- Retention of records and documentation
- Arrangements for data integrity maintaining
- Equipment validation, qualification and maintenance activities,
- Approving subcontractors,
- Personnel,
- Contact persons.
Quality agreements are typically developed during the negotiation of a commercial agreement with a supplier. Since often in parallel with the quality agreement, there are several other topics to be agreed upon that are not within its scope, it might be helpful to refer to a separate document relating to the same subject matter, covering different aspects of the cooperation (for instance financial) between the parties.
What activities are not covered by quality agreement?
As a general rule, the quality agreement shall not involve business arrangements between the parties. The terms and conditions related to intellectual property, confidentiality, remuneration or liability also usually go beyond of the scope of quality technical agreements (TQA) and are regulated in separate commercial contracts, such as Master Service Agreements or Supply Agreements. Nevertheless, commercial contracts and quality agreements should not be “stand alone” documents but have to complement each other instead – as they deal with different aspects of the same activities.
Below we present the comparative table outlining the main differences between commercial contracts and quality agreements in business relationships:
Category | Commercial Contract | Quality Agreement |
Purpose | Specifies terms of sale of goods or services | Establishes quality standards and quality control procedures |
Parties | Typically between the company and the client / partners | Usually between suppliers and recipients of goods or services |
Clauses | Concerning prices, payment terms, delivery terms | Focused on meeting specific quality standards, testing procedures, and inspection |
Responsibility | Associated with delivering goods or providing services | Relates to ensuring quality and compliance with GMP standards |
Penalties | Related to breach of contract terms, such as contractual penalty | May include penalties for failure to meet quality standards or non-compliance |
For the above reason, both of them should be carefully worded and reviewed in order to maintain consistency and avoid any confusion or discrepancies. While they may overlap in certain operational areas, it would serve the best interest of each party, if the provisions did not duplicate but rather were incorporated into one another by reference. It is important to keep in mind that the wording throughout both documents as well as the agreements’ duration to be unified and preferably, also the parties thereto.
Why do you need a quality agreement?
Establishment of technical quality aspects during the collaboration in the pharmaceutical industry is a key element in ensuring product safety. Quality agreements are necessary to ensure compliance with industry standards and regulations, first and foremost, compliance with legal requirements. The GMP requires manufacturers and importers of medicinal products to take all the necessary steps to guarantee the safety, effectiveness and quality of their products. In addition, cGMP directly obliges manufacturers to discuss and agree with the suppliers on the quality requirements for starting materials and appropriate aspects should be documented in a formal quality agreement or specification [4]. A carefully worded, readable and thought-through quality agreement would not only ensure that each party involved in the manufacturing understand each other correctly in every technical detail, but also minimize any potential problems or errors that could possibly lead to regulatory deficiencies.
It is also important to keep in mind that since the quality agreements are required by the GMP, they can be examined during inspections by the competent authorities. As a consequence, it would be worth establishing beforehand what areas of the cooperation between the parties should be disclosed in such a contract. The primary issue that would be of interest to the authority during such inspection is how the parties have allocated the GMP roles and responsibilities among themselves. A legible, well-scripted technical agreement provides a convenient template with answers at hand to the inspectors’ questions.
A simple explanation of why is the quality agreement so important lies in cGMP, describing “the contract giver is responsible for ensuring by means of the contract that the principles and guidelines of GMP are followed” [5]. On the one hand, the Technical Quality Agreement sets the legal obligations of adherence to established standards, but let us note that in the end, in the pharmaceutical industry it is also a primary value, which is the health safety of the final recipients, i.e. patients.
[1] Contract Manufacturing Arrangements for Drugs: Quality Agreements Guidance for Industry, U.S. Food and Drug Administration, November 2016, https://www.fda.gov/media/86193/download, p. 6
[2] EU Guidelines for GMP for Medicinal Products for Human and Veterinary Use, Chapter 7: Outsourced Activities, https://health.ec.europa.eu/document/download/58b5106a-cf6f-4352-9dca-1caf5d27d97e_en?filename=vol4-chap7_2012-06_en.pdf, 7.15
[3] Contract Manufacturing Arrangements for Drugs: Quality Agreements Guidance for Industry, U.S. Food and Drug Administration, November 2016, https://www.fda.gov/media/86193/download, p. 6
[4] EU Guidelines for GMP for Medicinal Products for Human and Veterinary Use, Chapter 5: Production, https://health.ec.europa.eu/document/download/4a1fdb4f-6f6f-49c4-b264-8056e5bbe078_en?filename=chapter_5.pdf, 5.28
[5] EU Guidelines for GMP for Medicinal Products for Human and Veterinary Use, Chapter 7: Outsourced Activities, https://health.ec.europa.eu/document/download/58b5106a-cf6f-4352-9dca-1caf5d27d97e_en?filename=vol4-chap7_2012-06_en.pdf, 7.5